JUAN PABLO GONZÁLEZ GARCÍA
Responsable de la Oficina técnica del Grupo Puma. Arquitecto, especialidad Edificación. ETSA Sevilla (2002). Dilatada experiencia en patología y cálculo de estructuras de edificación, así como en asesoramiento técnico-comercial de productos y sistemas aplicados en el sector de la construcción, sobre todo los vinculados al mundo de la reparación y el refuerzo estructural, impermeabilizaciones, rehabilitación patrimonial y rehabilitación energética en edificación.
LA IMPORTANCIA DEL INCREMENTO DE LA DURABILIDAD EN LAS ESTRUCTURAS DE HORMIGÓN ARMADO. TIPOS DE ATAQUES
La durabilidad referida al hormigón armado es la capacidad que tiene el material para soportar los ataques físicos y químicos a lo largo de su vida útil y llegar al final de esta con un coeficiente de seguridad que pueda considerarse aceptable para el uso y la clase de exposición para los que se proyectó. Es un tema de vital importancia en el articulado de las nuevas normativas de ámbito estructural (Código Estructural), ya que se persigue prolongar al máximo la vida útil de las estructuras con la premisa de que resulta más sostenible y económico reparar e incrementar la protección de las estructuras existentes para aumentar su vida útil, que demolerlas y construirlas de nuevo al concluir su vida útil.
En función de la clase de exposición, la normativa define las características que deben cumplir los hormigones fundamentalmente en cuanto a contenido mínimo en cemento, relación agua/cemento y recubrimientos de armaduras adecuados. Cada elemento de hormigón se encuentra sometido a diferentes agentes agresivos, en función de su clase de exposición ambiental, comprometiendo su durabilidad con el paso del tiempo.
Los ataques que puede sufrir un elemento de hormigón armado pueden ser de diferentes tipos (fig. 1):
- Corrosión por carbonatación
- Corrosión por cloruros
- Reacción árido-álcali
- Ataque sulfático
- Ataque por ciclos de hielo-deshielo
- Ataque por erosión
- Ataque ácido
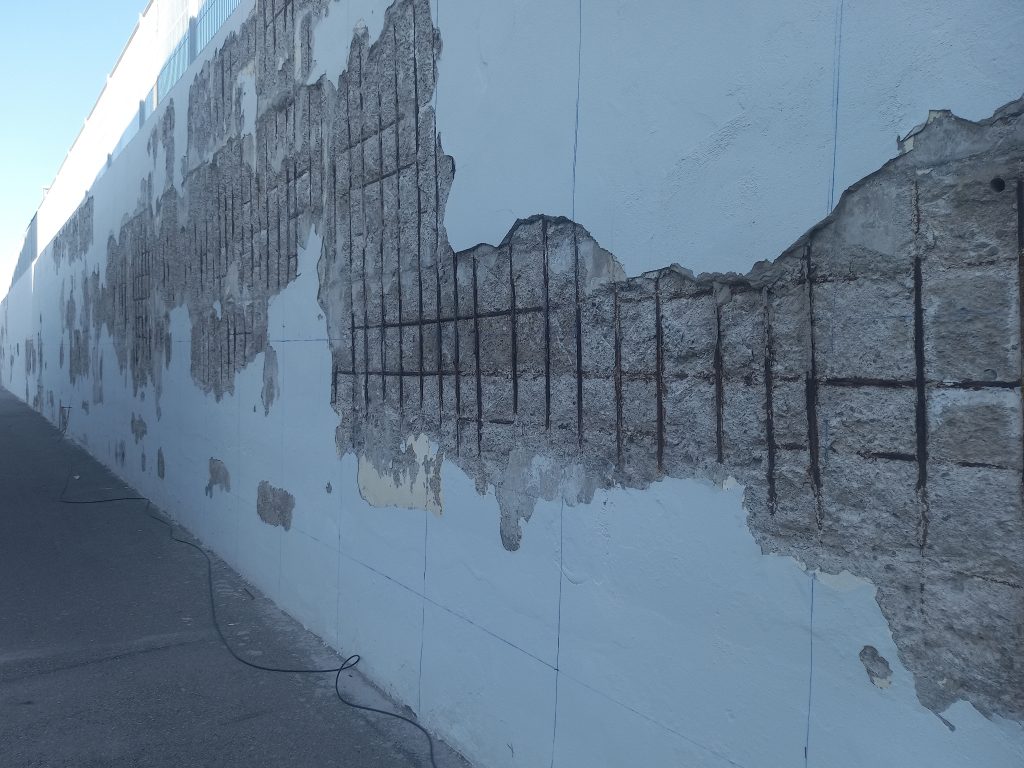
Figura 1. Muro de hormigón armado con daños severos
En la mayoría de estos ataques, el agua está íntimamente involucrada, al transportar las sustancias agresivas a través de los poros del hormigón o posibilitar las reacciones químicas que provocan los ataques que acaban afectando a las armaduras (medio acuoso que permite la movilidad de electrones entre la zona anódica y la zona catódica que componen la pila electroquímica, necesaria para que exista corrosión del acero), por lo que podemos afirmar categóricamente que impidiendo la penetración del agua en la sección estructural de hormigón armado lograremos ampliar su vida útil al disminuir drásticamente el tiempo necesario para que se produzca la corrosión del acero, por lo que las medidas de protección irán encaminadas fundamentalmente a dificultar lo máximo posible la penetración del agua y, adicionalmente, la difusión del dióxido de carbono y los cloruros mediante:
- La reducción de la porosidad del hormigón.
- La ejecución de barreras físicas en la superficie del hormigón.
- La reparación del hormigón empleando pasivadores y morteros especialmente formulados.
El avance de la corrosión en las armaduras produce una disminución de la capacidad portante y el coeficiente de seguridad de la estructura hasta incluso alcanzar su estado límite último, produciéndose: pérdida de sección de las barras, disminución de la adherencia al hormigón, fisuración del hormigón y debilitación e incluso rotura de las armaduras, especialmente delicado en el caso de barras pretensadas. En casos extremos se puede producir incluso el colapso parcial o total de la estructura afectada.
Todas estas circunstancias, hacen necesario revisar periódicamente el estado de conservación de los elementos estructurales realizados con este material para implementar las medidas preventivas o correctivas necesarias según su grado de importancia.
Corrosión por carbonatación
La carbonatación afecta a todo hormigón una vez desencofrado. Inicialmente, el PH del hormigón suele mantenerse entre 12,5 y 13,5 gracias a los hidróxidos alcalinos de calcio, sodio y potasio presentes en los poros. Cuando penetra el dióxido de carbono atmosférico a través de la porosidad natural del hormigón, éste reacciona con la fase líquida de hidróxido cálcico contenido en los poros y con las fases hidratadas del cemento. El proceso de carbonatación se produce por la reacción de dicho compuesto con el dióxido de carbono atmosférico para formar carbonato cálcico, lo que supone un aumento de volumen en torno al 11%, ocupando éste parte de los poros y densificando el hormigón.
Al mismo tiempo, el pH va decreciendo hasta valores inferiores a 9, despasivando las barras de acero embebidas en el hormigón. El proceso de carbonatación depende de varios factores, como pueden ser: la porosidad del hormigón, la concentración de dióxido de carbono en el ambiente (mayor en zonas urbanas e industriales), la humedad relativa y la cantidad de sustancia a carbonatar.
Una mayor relación agua/cemento conlleva una mayor porosidad del hormigón, favoreciendo la carbonatación. La humedad relativa ideal para la carbonatación se sitúa en el rango entre el 50-70%. Hormigones muy secos o saturados de agua impiden o ralentizan mucho el fenómeno de la carbonatación, que es un proceso habitualmente muy lento y que disminuye con el tiempo.
La corrosión en las barras se traduce en una pérdida de sección aproximadamente uniforme que el técnico redactor del proyecto puede valorar como admisible, teniendo en cuenta la disminución del coeficiente de seguridad de la estructura, o como no admisible, por lo que se deberán plantear soluciones de refuerzo estructural en este caso.
Mediante la aplicación de fenolftaleína o timolftaleína, que son indicadores colorimétricos del PH, se puede diagnosticar fácil y rápidamente la profundidad del frente de carbonatación, ya que estas sustancias se vuelven transparentes en contacto con superficies cuyo PH es inferior a 9, indicando que la zona está carbonatada. Las zonas no carbonatadas se mantendrán con la coloración púrpura de las mencionadas sustancias.
El Código Estructural en el Anejo 12 “Estimación de la vida útil de elementos de hormigón”, de carácter informativo, proporciona modelos de cálculo para el período de iniciación de la corrosión en elementos de hormigón para los casos de carbonatación y de ingreso de iones cloruro en el hormigón.
Corrosión por cloruros
Los iones cloruro pueden estar presentes en el hormigón debido a los diferentes materiales empleados en su fabricación o porque penetren desde el exterior a través de la red porosa mediante difusión, que suele ser lo más habitual en ambientes marinos y también en zonas donde se emplean sales de deshielo o sustancias químicas.
El componente fundamental en la unión química de los cloruros es el aluminato tricálcico. Éste reacciona con los iones cloruro formando el monocloroaluminato hidratado y el tricloroaluminato hidratado. El cloruro libre es el más dañino desde el punto de vista de la corrosión, ya que queda disuelto en el agua y puede ser transportado a través de la red de poros, llegando a despasivar la armadura, iniciando la corrosión.
La penetración de cloruros en los primeros centímetros del recubrimiento de la sección de hormigón depende principalmente de la absorción capilar, mientras que la penetración a profundidades mayores se basa en la difusión a largo plazo. La solución con cloruros se absorbe por las microfisuras y poros vacíos de la superficie, penetrando hacia el interior por succión capilar. Si existe humedad en la superficie, la entrada inicial se produce por permeabilidad o difusión.
La corrosión por cloruros en las barras de acero embebidas en el hormigón se caracteriza por ser anárquica, ya que no sigue un patrón regular y su peligrosidad radica en que puede llegar a seccionar completamente las barras en determinados puntos.
Reacción árido-álcali
Solo se produce en hormigones propensos a padecerla, debido al carácter reactivo de los áridos empleados en su fabricación. Está provocada por iones hidroxilos que reaccionan con ciertas fases reactivas de los áridos en presencia de humedad. Ya en disolución, la sílice reacciona con los álcalis para formar el gel árido – álcali, que es de tipo higroscópico, absorbe agua y aumenta de volumen, provocando tensiones internas en el hormigón que producen fisuras y desprendimientos. El agua juega un papel esencial en el desarrollo de la reacción árido-álcali, ya que es el medio necesario para que se desplacen los reactivos involucrados (iones alcalinos e hidroxilos), y porque es absorbida por el gel higroscópico que se produce en la reacción. Dicho gel expande y provoca las tensiones internas que produce las fisuras en el hormigón, las cuales generan nuevos caminos de penetración de humedad del exterior y posibilitan que la reacción se prolongue en el tiempo. Los síntomas más habituales que se observan en una estructura afectada por este tipo de ataque serían:
- Fisuraciones superficiales en forma de mapa o siguiendo la disposición de los armados.
- Desprendimientos en la superficie del hormigón.
- Aparición de gel blanquecino en la superficie del hormigón.
Estos síntomas no son concluyentes y pueden ser debidos a otras causas, por lo que suele ser necesario realizar una observación en el microscopio electrónico del hormigón deteriorado para corroborar el diagnóstico de la afección por reacción árido-álcali. Las medidas preventivas más habituales son:
- Uso de áridos no reactivos.
- Uso de cementos con bajo contenido en álcalis.
- Limitación de la entrada de agua en el hormigón mediante la aplicación de un protector superficial.
Ataque sulfático
El ataque sulfático se compone de una serie de reacciones que se producen entre los iones sulfato y compuestos del cemento hidratado en hormigones endurecidos. Estas reacciones conllevan la formación de yeso, ettringita secundaria y thaumasita. La ettringita que se produce en un hormigón endurecido se denomina ettringita secundaria, cuya formación produce expansiones internas y debilitamiento dentro de la matriz, que son las patologías más comunes asociadas a este tipo de ataque. La ettringita primaria (necesaria y deseada), se forma durante la hidratación del cemento al añadir yeso como retardador de fraguado, cuyos sulfatos reaccionan con los aluminatos cálcicos para disminuir el calor de hidratación. Cuando se emplea cemento portland ordinario en el hormigón (no sulforresistente), se forma ettringita secundaria, que es extremadamente expansiva, como resultado de la reacción entre los sulfatos y los aluminatos del cemento. En ciertas circunstancias, se puede formar también thaumasita, causando más daño a la estructura. Más que su poder expansivo en la matriz de cemento hidratado, lo más perjudicial de la aparición de la thaumasita es que el hormigón se convierte en una masa sin consistencia que se desmenuza a la mínima presión, afectando a su resistencia estructural. La solución para evitar este tipo de ataque se basa en:
- El empleo de hormigones y/o morteros de reparación sulforresistentes.
- La formulación de hormigones con baja relación agua/cemento, que minimiza la porosidad del hormigón, dificultando la penetración de sulfatos.
- La ejecución de protectores superficiales del hormigón que eviten la acumulación de agua con elevados contenidos en sulfatos y su ingreso al interior del elemento estructural.
Ataque por ciclos de hielo y deshielo
El hormigón es un material poroso que absorbe agua. Cuando ésta se congela, se expande, creando presiones internas en los poros del hormigón. La repetición de este mecanismo en elementos situados a la intemperie puede dar lugar a una serie de fenómenos de degradación por ciclos de hielo-deshielo, produciendo agrietamientos, descamaciones y desconchones en la superficie del hormigón. Dichas afecciones provocan un aumento de la aspereza y de la porosidad superficial, haciendo que el fenómeno se retroalimente con el paso del tiempo, volviéndose más agresivo y produciendo una disminución del espesor de recubrimiento de las armaduras, así como una mayor entrada de agua en la estructura, provocando corrosión y afectando a integridad de las armaduras. Las medidas preventivas más habituales para combatir este tipo de ataque son:
- Formulación adecuada del hormigón para conseguir porosidad muy reducida (baja relación agua/cemento, alto contenido en cemento, áridos de calidad y tamaño adecuados).
- Uso de aditivos aireantes en el hormigón, que crean una serie de pequeñas burbujas de aire en la matriz del hormigón, proporcionando espacio para la expansión del agua helada sin que se creen presiones internas excesivas.
- Limitación de la entrada de agua en el hormigón mediante la ejecución de un protector superficial.
Ataque por erosión
La erosión es el desgaste que se produce en la superficie de las estructuras de hormigón debido a fuerzas mecánicas causadas por el movimiento de objetos, maquinaria, tráfico peatonal o vehicular sobre la superficie de hormigón. Dicha abrasión puede provocar una pérdida gradual de la capa de rodadura del material, debilitándola, y produciendo rugosidad en la superficie, generación de polvo e incluso pérdida de lechada que acaba exponiendo los áridos del hormigón. Para evitar este tipo de ataque se recomienda:
- Formular adecuadamente el hormigón según la clase de exposición XM: Adecuado contenido en cemento, correcta relación agua/cemento, empleo de áridos finos silíceos o equivalentes y curado prolongado.
- Emplear productos para la mejora de la capa de rodadura por espolvoreo o de tipo líquido (mineralizadores de litio).
- Diseño de acabados lo más lisos posible.
- Aplicación de revestims lisos posiblesientos o resinas de protección para mejorar la cohesión de la capa de rodadura y la resistencia a la abrasión.
- Mantenimiento adecuado y limpieza para eliminar objetos sueltos en superficie.
Ataque ácido
Los hormigones pueden también ser atacados por otros compuestos químicos como las aguas ácidas (residuales, con elevado contenido en fertilizantes), aguas puras (aquellas procedentes de manantiales, con elevado poder de disolución), magnesio y amonio, siendo el más habitual el producido por aguas ácidas y puras. Inicialmente se disuelve la portlandita y después se produce el ataque al aluminato cálcico, siendo esta disolución muy lenta debido a las solubilidades limitadas de los reactivos. Se suele producir cuando el hormigón está en contacto con agua de escorrentía o flujo permanente, que no permite que ésta se sature y, por tanto, siga disolviendo componentes del hormigón. Los ácidos aceleran el proceso de degradación del hormigón debido al PH bajo (siendo más graves cuanto más bajo sea dicho PH), llegando a atacar a los áridos calcáreos y siendo más resistentes los de naturaleza silícea. Cuando los ácidos alcanzan las armaduras, comienza la corrosión de las mismas y la fisuración del hormigón. Para evitar el ataque ácido se pueden emplear:
- Hormigones muy densos con recubrimientos elevados y cementos resistentes a sulfatos.
- Protectores superficiales del hormigón resistentes a los ácidos.
ACCIONES PREVENTIVAS: INHIBIDORES DE CORROSIÓN MIGRATORIOS
Las acciones preventivas están destinadas a prevenir los posibles daños ocasionados por los ataques físicos o químicos, antes de que éstos se produzcan. Para ello, GRUPO PUMA dispone de una gama de productos de inhibidores de corrosión migratorios basados en la tecnología de aminas (aminoalcoholes y aminocarboxilatos).
Los inhibidores de corrosión migratorios son productos químicos en formato líquido que se aplican sobre la superficie del hormigón endurecido mediante rodillo o airless, en una o dos capas habitualmente y que proporcionan los siguientes beneficios (fig. 2):
- Penetran al interior de la sección de hormigón armado a través de la propia porosidad del hormigón.
- Migran hacia las armaduras existentes, deteniendo la corrosión en dichos elementos.
- Poseen efecto hidrofugante en la superficie del hormigón, sellando parcialmente los poros y reduciendo la entrada de agua.
- Incrementan la resistividad, se detiene el movimiento de electrones que provoca la corrosión en el acero.
- Reducen la difusión de oxígeno y de dióxido de carbono, por lo que también realizan cierto efecto protector contra la carbonatación.
- Tienen una capacidad de penetración de entre 3 y 9 cm, aproximadamente, en función de las características del hormigón soporte.
- Son habitualmente incoloros. Puede verificarse su correcta aplicación empleando luz ultravioleta.
- Poseen una elevada durabilidad. Existen edificios monitorizados desde hace más de 20 años y aún perdura su eficacia.

Los inhibidores MCI realizan su acción mediante tres pasos: Acción capilar, fase vapor y adsorción física. Poseen certificado de conformidad del control de producción en fábrica según lo indicado en la normativa EN 1504-2:2004 (Sistemas de protección para el hormigón) y EN 1504-7:2006 (Productos y sistemas para la protección frente a la corrosión), bajo sistema 2+, emitido por APPLUS:
Morcemrest inhibidor AA 2021 (MCI)
MORCEMREST INHIBIDOR AA 2021 (MCI) es un inhibidor de corrosión migratorio de superficie base aminoalcohol, que utiliza una mezcla de silicatos reactivos, agentes activadores de superficie al mismo tiempo que inhibidores de corrosión migratorios. Se encuentra formulado para preservar y proteger el hormigón usando la propia química del hormigón. Los silicatos reactivos penetran en el hormigón algo más de 38 mm reaccionando con el hidróxido cálcico para formar unos productos de reacción que originan más estructuras de silicato insoluble dentro del hormigón. Estas estructuras incrementan la densidad del hormigón, sellan los poros de la superficie e impermeabilizan la superficie. Estas nuevas estructuras realizan la función de barrera a la penetración del ion cloruro y el ataque por carbonatación, protegiendo además del ataque ácido y alcalino, no viéndose afectada la capacidad de difusión vapor. Está diseñado para migrar a través de los poros de la estructura y buscar el metal embebido en la misma., protege también refuerzos de acero, acero al carbono, acero galvanizado, el aluminio y otros metales. Una característica única de los Inhibidores migratorios de corrosión es que, si no están en contacto directo con los metales, el inhibidor migrará una distancia considerable a través del hormigón para proporcionar protección. MORCEMREST INHIBIDOR AA 2021 (MCI) detiene la corrosión de los metales y extiende el servicio de la estructura.
Morcemrest inhibidor CX 2020 (MCI)
MORCEMREST INHIBIDOR CX 2020 (MCI) es un inhibidor de corrosión migratorio de superficie diseñado para penetrar a través de materiales cementosos incluyendo el hormigón, morteros y caliza. Migra a través de su fase líquida y vapor a través de los poros de la estructura, formando una capa monomolecular protectora sobre la armadura. Detiene la corrosión de los metales y extiende el servicio de la estructura, frente a los fenómenos de carbonatación, cloruros y otros contaminantes. Test realizados muestran una reducción de la corrosión cuando el hormigón tiene un alto contenido en cloruros (fig. 3).

ENSAYOS REALIZADOS CON INHIBIDORES DE CORROSIÓN MIGRATORIOS
Informe 22 – 1 / Contracto CM – 19 – 11 realizado por el IETcc: estudio de la actividad de los inhibidores de corrosión frente a los procesos de corrosión por ion cloruro.
Antecedentes
En Febrero de 2011, se solicitó al Centro de Investigación en Seguridad y Durabilidad Estructural y de Materiales (CISDEM), ubicado en el Instituto de Ciencias de la Construcción Eduardo Torroja (IETcc), la realización de un estudio sobre la efectividad de inhibidores frente a los procesos de corrosión.
Objecto del informe
El objetivo del informe es el estudio de la actividad de varios inhibidores aplicados sobre el hormigón, suministrados por el peticionario, sobre los procesos de corrosión debido a la acción de los iones cloruros. Estos inhibidores actúan aplicados en superficie. El ensayo compara su actividad en los procesos de corrosión frente al mismo hormigón sin tratar con inhibidor.
Ensayo realizado
El ensayo efectuado fue:
- El ensayo efectuado fue: • Ensayo integral acelerado de corrosión por penetración de cloruros: Estos ensayos permiten evaluar la resistencia al ingreso de los iones cloruro definido por el coeficiente de difusión en estado no estacionario, la concentración crítica de estos iones que provocan la corrosión de la armadura, y el progreso de la corrosión de la armadura mediante la medida de su velocidad.
Probetas estudiadas
Los inhibidores líquidos AA y CX fueron aplicados en la superficie de las probetas del hormigón patrón (una sola cara) tras 28 días de curado y 6 días en condiciones de laboratorio, aplicando una dosificación de productos de 0,27 l/m2 de superficie de hormigón. Tras la aplicación, las probetas permanecieron en condiciones de laboratorio 3 meses, antes de la realización de los ensayos. Según el tipo de ensayo realizado, se emplearon los siguientes tipos de probetas de hormigón:
- Ensayo de durabilidad del hormigón. Penetración de cloruros en el hormigón y corrosión en la armadura. Método integral acelerado (PrUNE 83992): Probetas prismáticas de 7 x 7 x 7 cm incorporando una barra de acero corrugado.
Los aceros embebidos en las probetas fueron aceros corrugados M-600, los cuales antes de ser embebidos fueron limpiados, decapados y protegidos con cinta aislante con el fin de que la superficie de contacto con el hormigón se mantuviera constante en 5,65 cm2. Todas las probetas fueron curadas 28 días en cámara húmeda a 21°C de temperatura y humedad relativa mayor del 95%.
Descripción del ensayo realizado – Método integral de penetración de cloruros
El ensayo consiste en exponer una probeta de hormigón, en la que se ha embebido transversalmente una barra de acero al carbono, a una corriente eléctrica por medio de dos electrodos uno colocado en una disolución de cloruro sódico y cúprico introducida en un recipiente ubicado en una cara de una probeta cúbica de hormigón, y el otro electrodo colocado en la cara opuesta. Los iones cloruro penetran de forma acelerada debido a la acción del campo eléctrico y migran desde el recipiente hasta el electrodo en la parte inferior encontrando en su camino al acero, al que corroen (fig. 4).
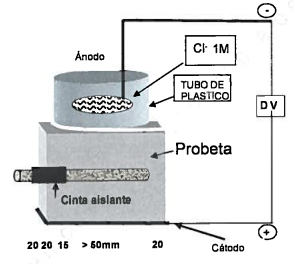
Se registra el tiempo desde que se conecta el campo eléctrico hasta la despasivación del acero, que es indicativo del coeficiente de difusión en estado no estacionario. Se registra el valor de la carga en culombios que ha dado lugar a la corrosión. Se desconecta la corriente y una probeta se rompe, obteniéndose muestras de la parte cercana a la armadura en la cara más cercana a la piscina con cloruros y de la superficie donde estaba la piscina colocada, para analizar respectivamente la concentración crítica de cloruros que ha producido el inicio de la corrosión, así como la concentración superficial de cloruros. En otra probeta se continúa el ensayo desconectando la corriente, para producir una cierta corrosión del acero con el fin de obtener valores de la velocidad de corrosión de la barra embebida.
Resultados – Penetración de cloruros mediante el método integral
Se presentan: el tiempo de despasivación medio (en días), la velocidad de corrosión alcanzada al corroer la armadura (Icorr), y los % de mejora en la concentración crítica (Ccrit) de cloruros que producen la despasivación y los coeficientes de difusión calculados según la formulación propia de cada ensayo. Dado que la concentración crítica de cloruros que produce la despasivación es específica para cada tipo de hormigón fabricado, se ha optado por reflejar el % de mejora de las probetas con inhibidor frente a la probeta patrón o probeta sin inhibidor (tabla 1).

Tabla 1.
Conclusiones de los ensayos realizados
- El efecto más significativo se ha observado en la propagación de la velocidad de corrosión obtenida en condiciones naturales (tras la despasivación en el ensayo acelerado de cloruros), donde el uso de inhibidores reduce entre un 40 y 80% (dependiendo el tipo de inhibidor) la velocidad de corrosión y con ello, la pérdida de sección calculada.
- La tecnología empleada en Morcemrest Inhibidor CX 2020 (MCI) se ha mostrado más eficaz que la empleada en Morcemrest Inhibidor AA (2021 (MCI), obteniendo en el ensayo realizado mejores resultados en cuanto a tiempo de despasivación del acero, velocidad de corrosión del acero, pérdida de sección de las barras durante el tiempo de duración del ensayo y % de mejora frente a un hormigón patrón en el que no se han aplicado inhibidores de corrosión.
- Mediante el empleo de ambos inhibidores de corrosión, se ha conseguido una mejora significativa en la protección del acero, en comparación con el hormigón sin proteger.
ACCIONES PREVENTIVAS: REVESTIMIENTOS DE PROTECCIÓN SUPERFICIAL SEGÚN NORMA UNE EN 1504-9
Como se ha comentado anteriormente, si conseguimos que el agua, el dióxido de carbono y los cloruros no penetren en el interior de la sección de hormigón armado, habremos conseguido evitar la gran mayoría de las agresiones que sufre el material. Los revestimientos son barreras de protección que pueden emplear los proyectistas, entre algunas otras opciones en función del fin perseguido, según la norma UNE EN 1504 para realizar diferentes mejoras sobre la superficie del hormigón a proteger (tabla 2).
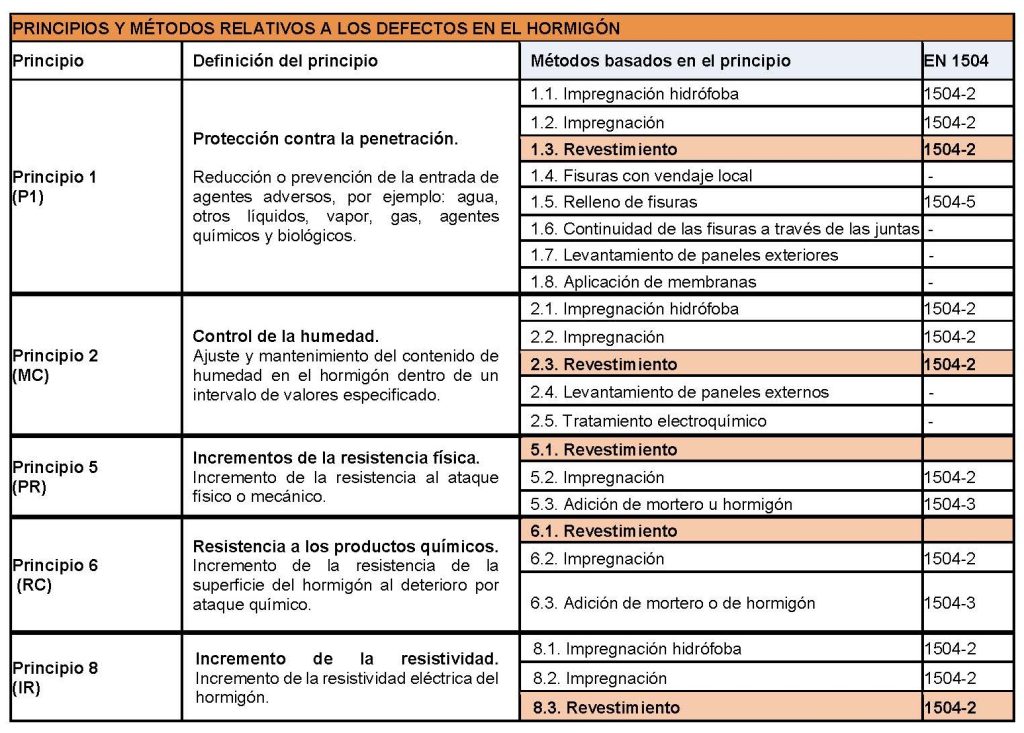
Tabla 2. Principios y métodos relativos a los defectos en el hormigón
Los revestimientos son tratamientos del hormigón destinados a producir una capa protectora continua en su superficie y poseen las siguientes características:
- Los poros de la superficie están totalmente rellenos.
- Alteran el color y la textura de la superficie.
- Película delgada continua (0,1 a 5 mm habitualmente).
- Clasificación:
- Polímeros orgánicos.
- Polímeros orgánicos + cemento.
Tipos de revestimientos estancs cimentosos del Grupo Puma
Los revestimientos estancos cementosos son productos muy versátiles, ya que pueden emplearse tanto en edificación como en obra civil como protectores superficiales del hormigón, estableciendo una barrera contra la penetración de sustancias agresivas que producen la degradación del hormigón, tales como agua, cloruros y dióxido de carbono, posibilitando así una mayor durabilidad de las estructuras de hormigón. Otro uso habitual en este tipo de productos es la impermeabilización, tanto de depósitos y aljibes de agua potable como de muros de sótano, muros de contención, piscinas, arquetas, terrazas y pequeñas cubiertas. Poseen certificado de potabilidad, lo cual permite que estén en contacto directo con agua destinada al consumo humano y, al mismo tiempo, protegen el agua almacenada de su posible contaminación por filtración de agua procedente del terreno, debido a que estos productos trabajan impermeabilizando tanto a presión positiva como negativa (fig. 5). Grupo Puma posee los siguientes revestimientos cementosos englobados en su gama Morcem Dry. Poseen certificado de conformidad del control de producción en fábrica según lo indicado en la normativa EN 1504-2:2005 (Sistemas de protección para el hormigón), bajo sistema 2+, emitido por APPLUS:
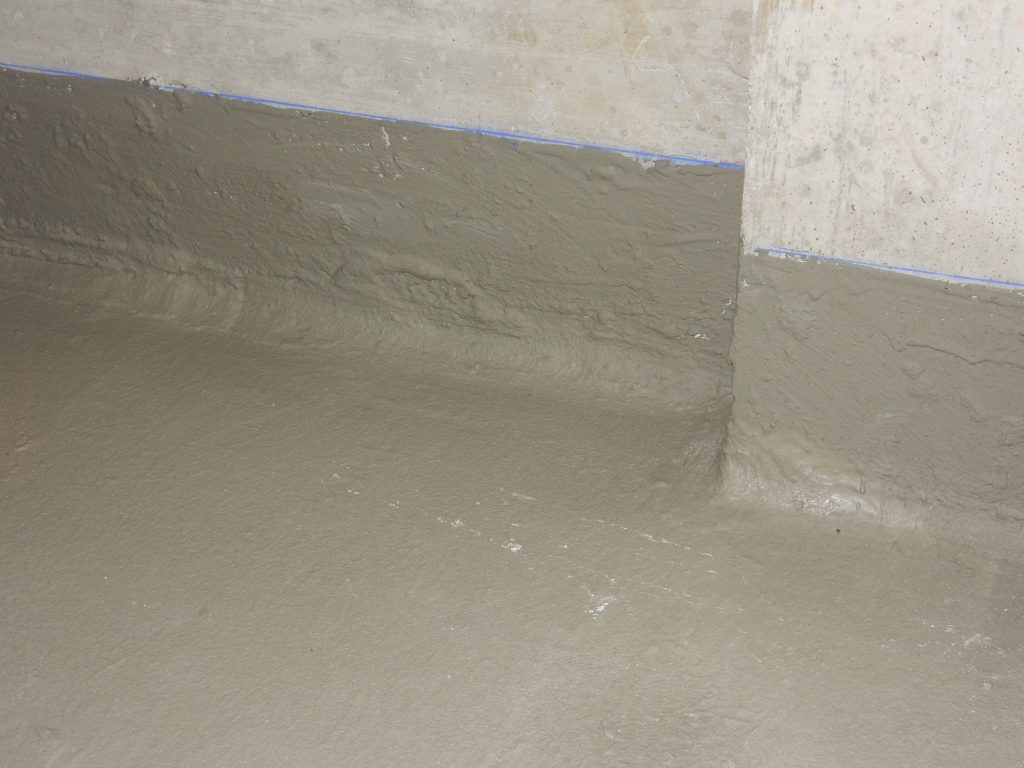
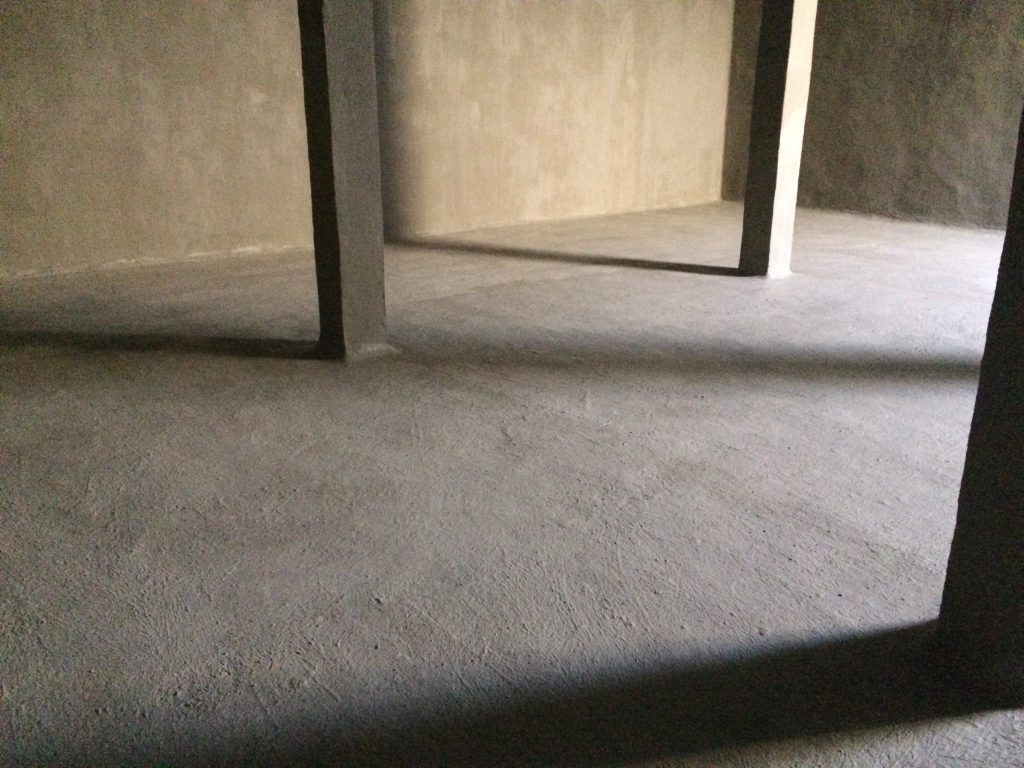
Morcem Dry F
Es un mortero cementoso flexible bicomponente a base de ligantes hidráulicos y resinas sintéticas, para impermeabilización del hormigón según Norma UNE-EN 1504-2. (Sistemas de protección superficial para el hormigón). Para garantizar la estanqueidad al paso del agua, se precisa la aplicación con rodillo, brocha o airless sobre el soporte a impermeabilizar y/o proteger de 2 manos de 1 mm de espesor cada una. Mediante su armado con la Malla Drypool, de fibra de vidrio antiálcalis, se aumenta la resistencia a la fisuración del revestimiento, requiriendo la aplicación de 1 mano adicional de 1 mm de espesor de Morcem Dry F para que la malla quede correctamente embebida en la sección del revestimiento de mortero estanco. Rendimiento: 1,5 Kg/m2/mm espesor. Características y aplicaciones:
- Permeable al vapor de agua.
- Resistente a heladas y deshielos.
- Excelente adherencia.
- No altera la potabilidad del agua. Es conforme con los requisitos establecidos en el Real Decreto 03/2023, por el que se establecen los criterios sanitarios de la calidad del agua de consumo humano.
- Alto rendimiento y flexibilidad permanente.
- Resistente a sulfatos en concentraciones débiles y medios no ácidos.
- Impermeabilizaciones de depósitos, balsas, piscinas, fuentes, sótanos, aparcamientos subterráneos, fosos de ascensores, túneles, etc.
- Impermeabilización interior de depósitos de agua potable.
- Impermeabilización y protección del hormigón frente a la carbonatación, ciclos de hielo y deshielos, ataque por cloruros en obras públicas, canales de riego, plantas depuradoras, desaladoras, puentes, etc.
- Impermeabilización de balcones y terrazas (25-50 m2 como máximo) Si nos encontramos juntas de partición o dilatación las trataremos con la banda BANDTEC. Y reforzar la superficie siempre con Malla Drypool.
- Impermeabilización en muros exteriores en cimentación.
- Reparación y protección de superficies expuestas a la acción del hielo y deshielo: voladizos, balcones, azoteas, terrazas, cornisas, etc.
- Impermeabilización de superficies susceptibles a los movimientos, con presiones hidrostáticas positivas y negativas.
Morcem Dry SF Plus
Es un mortero cementoso semiflexible bicomponente a base de cemento gris de alta resistencia, áridos seleccionados, aditivos especiales y resinas, para impermeabilización del hormigón según Norma UNE-EN 1504-2. Sistemas de protección superficial para el hormigón. Para garantizar la estanqueidad al paso del agua, se precisa la aplicación con rodillo, brocha o airless sobre el soporte a impermeabilizar y/o proteger de 2 manos de 1 mm de espesor cada una. Mediante su armado con la Malla Drypool, de fibra de vidrio antiálcalis, se aumenta la resistencia a la fisuración del revestimiento, requiriendo la aplicación de 1 mano adicional de 1 mm de espesor de Morcem Dry F para que la malla quede correctamente embebida en la sección del revestimiento de mortero estanco. Rendimiento: 2 Kg/m2/mm espesor. Características y aplicaciones:
- Impermeabilizaciones exterior e interior de estructuras de hormigón, mortero, bloque de hormigón expuestos a presión positiva, tales como depósitos, balsas, aljibes, piscinas, fuentes, etc.
- Protección de superficies expuestas a la acción del hielo y deshielo: voladizos, balcones, cornisas, elementos ornamentales, etc.
- Revestible con piezas cerámicas con PEGOLAND® FLEX.
- Pintable con pinturas elastómeras o morteros acrílicos: Gama MORCEMCRIL.
- Resistente a los ciclos de hielo-deshielo.
- Resistente a la carbonatación.
- Excelente Adherencia y resistencia.
- Mortero de comportamiento semiflexible en comparación a un mortero tradicional.
- Aplicación en interiores y exteriores.
- Impermeable al agua.
- Permeable al vapor de agua.
- Fácil mezclado y aplicación.
- No altera la potabilidad del agua. Es conforme con los requisitos establecidos en el Real Decreto 03/2023, por el que se establecen los criterios sanitarios de la calidad del agua de consumo humano.
ENSAYOS REALIZADOS A REVESTIMIENTOS ESTANCOS CEMENTOSOS
Informe núm. 22.443 realizado por el IETcc: ensayos para el estudio sobre la durabilidad que supone el uso de los morteros de revestimiento Morcem Dry F y Morcem Dry SF Plus en hormigones armados frente procesos de corrosión por penetración de agresivos (Cl– i CO2).
Antecedentes
El informe forma parte del contrato firmado entre el Instituto de Ciencias de la Construcción Eduardo Torroja (IETcc) del Consejo Superior de Investigaciones Científicas (CSIC) y Grupo Puma. Dicho contrato nace del interés de Grupo Puma por corroborar que sus productos contribuyen a la prolongación de la vida útil de las estructuras y para ello deben ser ensayados en condiciones extremas, al objeto de verificar su correcto desempeño y el cumplimiento de los parámetros para los que fueron diseñados.
Objecto del informe
El objeto del informe es el estudio del mortero impermeable Morcem Dry SF Plus frente a los procesos de corrosión por carbonatación y presencia de cloruros en probetas de hormigón. También se ha estudiado el mortero impermeable Morcem Dry F frente a los procesos de carbonatación en las mismas probetas de hormigón. Para ello, se han realizado probetas de hormigón con y sin los morteros de revestimiento impermeables Morcem Dry SF Plus y Morcem Dry F, comparando los parámetros relacionados con los fenómenos de carbonatación y presencia de cloruros y estudiando la efectividad de estos productos frente a los procesos de corrosión.
Ensayos realizados
Los ensayos efectuados fueron los siguientes:
- UNE 83992-2 EX: ensayo de penetración de cloruros en el hormigón. Método integral acelerad0t. Este ensayo tiene por objeto determinar los efectos de la mezcla de hormigón/mortero en la resistencia a la penetración de los iones cloruros, la concentración crítica de estos iones para provocar la corrosión de la armadura y el progreso de la corrosión de la armadura, mediante la medida de la velocidad de corrosión.
- UNE EN 12390-12: determinación de la resistencia a la carbonatación del hormigón. Método de carbonatación acelerada. Este ensayo mide la resistencia a la carbonatación del hormigón empleando condiciones de ensayo que aceleran la velocidad de carbonatación. Para ello las probetas permanecerán en cámara al 3% de CO2 durante 70 días.
Probetas estudiadas
Se fabricó un hormigón con cemento CEM I 45.5 R como soporte para la aplicación de los morteros impermeables de estudio en los laboratorios del IETcc. Tras su fabricación, las probetas de hormigón (soporte) se introdujeron en cámara de curado durante 24 horas (HR > 95% y Tª aprox. 20 ºC). Posteriormente, se desmoldaron y permanecieron en cámara de curado una semana, fecha en la que se aplicaron los morteros impermeables en superficie. Una vez aplicados los morteros de estudio sobre el soporte de hormigón, según indicaciones de sus respectivas fichas técnicas, permanecieron en condiciones de laboratorio (21 ± 2 ºC y 60 ± 10% humedad relativa) durante 20 días, fecha en la que comenzaron a realizarse los ensayos anteriormente indicados. Cabe destacar que en este caso se aplicó una capa de 2 mm de espesor de los morteros de recubrimiento estando del lado de la seguridad, ya que estos productos permiten un espesor total de aplicación de hasta 3 mm. Para el ensayo de carbonatación acelerada se emplearon probetas cilíndricas de 7.5×15 cm. Este ensayo se realizó con los morteros Morcem Dry SF Plus y Morcem Dry F. Para el ensayo de penetración de cloruros se emplearon probetas cúbicas de 7x7x7 cm con una barra de acero embebido Ø 6 mm. Únicamente se sometió a este ensayo el mortero Morcem Dry SF Plus (el de menores prestaciones técnicas de los dos morteros ensayados) (fig. 6).
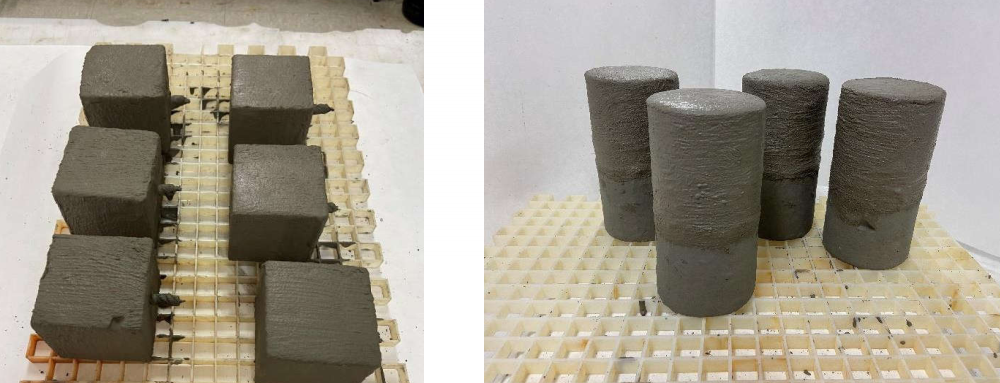
Ensayo de carbonatación acelerada al 3 % de CO2. Resultados
Tras la aplicación de los revestimientos Morcem Dry F y Morcem Dry SF Plus sobre el hormigón de referencia, el conjunto permaneció en condiciones de laboratorio durante 20 días, tiempo tras el cual se introdujeron durante 70 y 140 días dentro de una cámara climática al 3% de CO2. Trascurrido ese periodo las probetas de estudio se dividieron por la mitad en la dirección paralela a la cara fratasada. La profundidad de carbonatación se midió sobre la superficie recién fracturada. Cabe destacar que los morteros estudiados (Morcem Dry F y Morcem Dry SF Plus) fueron aplicados en cada mitad de una única probeta (fig. 7).

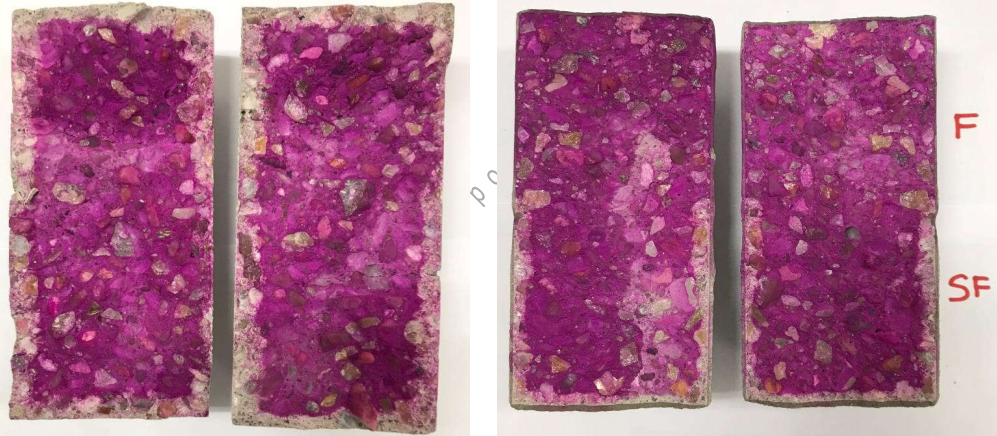
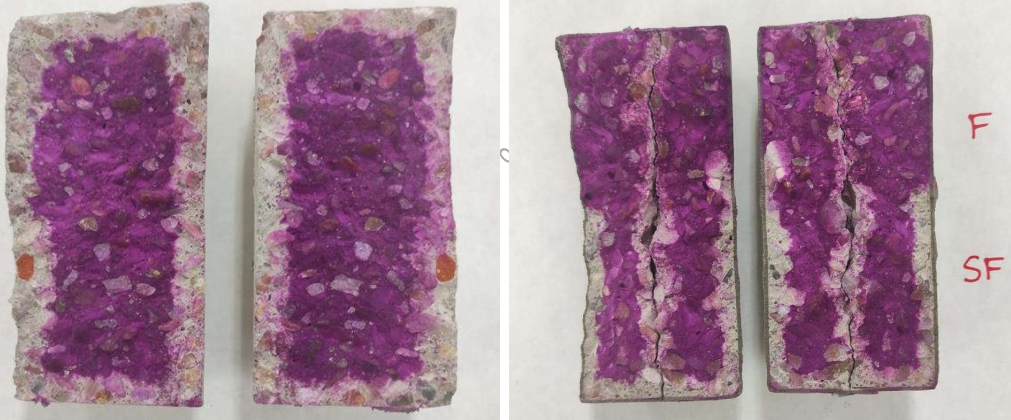
Observamos en las figuras 8 y 9 cómo no se ha detectado carbonatación tras 140 días de exposición acelerada en las probetas recubiertas con mortero Morcem Dry F. En las probetas recubiertas con Morcem Dry SF Plus, la profundidad de carbonatación obtenida ha sido inferior a la probeta de referencia. Por tanto, se puede concluir que el uso de los morteros de revestimiento empleados en el ensayo mejora significativamente las prestaciones frente a los procesos de carbonatación, siendo la presencia de carbonatación nula en el caso del uso del producto Morcem Dry F, tras una exposición a condiciones aceleradas de carbonatación de 140 días. En el caso del Morcem Dry SF Plus, esta mejora se sitúa en torno al 35% (figuras 10 y 11)
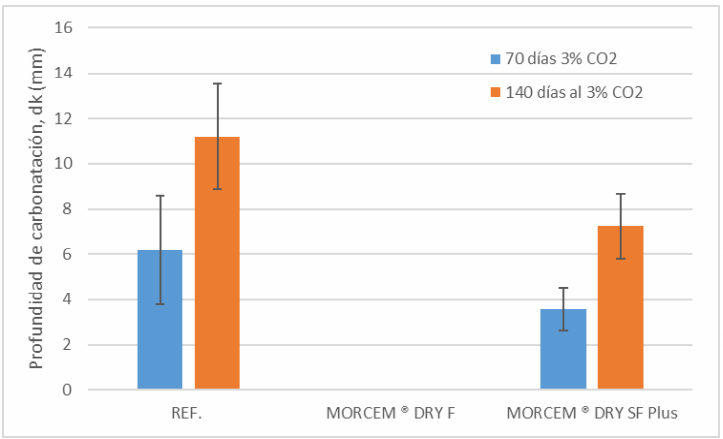
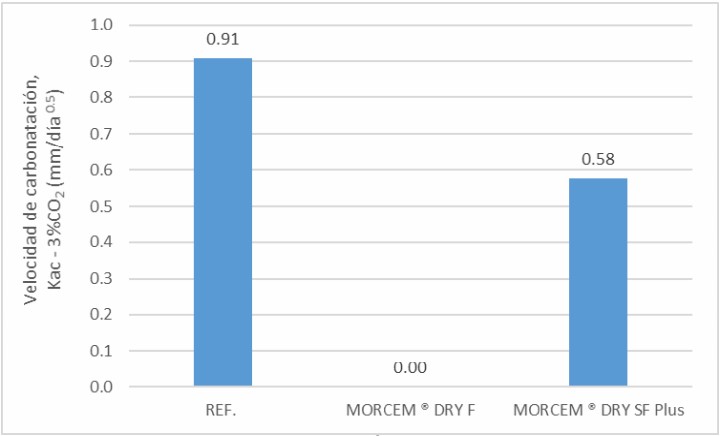
Ensayo de penetración de cloruros mediante ensayo acelerado integral. Resultados
Como se ha indicado anteriormente, en este caso, sólo se ensayó el mortero de revestimiento Morcem Dry SF Plus, con menores prestaciones técnicas que Morcem Dry F. Se midieron los tiempos de despasivación media (en días) y los coeficientes de difusión en estado no estacionario calculado a partir de las fórmulas incluidas en la norma UNE 83992-2 EX. En este caso, dado que el producto estudiado actúa como barrera para evitar la entrada de iones cloruros y, por tanto, no actúa sobre el hormigón, el coeficiente de difusión obtenido se identificó como coeficiente experimental de difusión (Dns, exp) que determina el coeficiente de difusión de los cloruros a través de los poros del hormigón y la barrera que ejerce el mortero Morcem Dry SF Plus al inicio de la corrosión. Se midió también la velocidad de corrosión acumulada en el tiempo tras los ensayos de propagación de la corrosión (ensayo sin aplicación de corriente en condiciones naturales), así como la concentración de cloruros en la cuna de acero (CCl) que se midieron al romper las probetas y extraer una muestra de hormigón en contacto con la superficie del acero despasivado. Asimismo, se calculó la penetración de la corrosión, Pcorr. Se observó que las resistencias eléctricas iniciales eran muy superiores en las probetas con mortero de revestimiento Morcem Dry SF Plus frente a las probetas referencia (sólo hormigón), lo que indica el efecto de mejora frente a la penetración de iones cloruro que posee Morcem Dry SF Plus. A mayores resistividades eléctricas, mayores propiedades durables del sistema frente a los procesos de corrosión. El coeficiente de difusión experimental obtenido con el uso del mortero de revestimiento Morcem Dry SF Plus mejoró frente a su probeta referencia (sólo hormigón) en un 50%, utilizando para el cálculo la siguiente ecuación:


Las medidas que se representan en la ilustración corresponden a las medidas de velocidad de corrosión (Icorr) en las probetas estudiadas. Las líneas grises horizontales punteadas representan el límite inferior y superior considerado para el umbral de despasivación del acero. Para valores superiores de 0.2 µA/cm2 el proceso de corrosión está activo. En la ilustración se puede observar como a los 3 días se produce la despasivación de las probetas referencia realizadas con hormigón estándar por efecto de la entrada de cloruros acelerados. Las probetas de hormigón con el revestimiento de mortero Morcem Dry SF Plus no se despasivaron hasta pasados 56 días de ensayo, lo que indica cómo el producto de estudio mejoró las prestaciones frente a la entrada de iones cloruro.
Conclusiones de los ensayos realizados
A la vista de los resultados de los ensayos realizados sobre el efecto de los morteros de revestimiento Morcem Dry F y Morcem Dry SF Plus, frente a los procesos de corrosión por carbonatación y presencia de iones cloruros en probetas de hormigón, se puede concluir que: Se observa un aumento muy significativo de la resistencia eléctrica del conjunto hormigón más mortero de revestimiento frente al hormigón referencia, lo que conlleva un aumento de la durabilidad frente a la corrosión por entrada de iones cloruro y carbonatación. Ensayo de carbonatación acelerada al 3% CO2: La velocidad de carbonatación para el hormigón con mortero de revestimiento Morcem Dry SF Plus ha disminuido en un 35% respecto al hormigón referencia (sin ningún tipo de recubrimiento adicional). En el caso de las probetas recubiertas con mortero Morcem Dry F no se ha observado carbonatación, por lo tanto, su velocidad de carbonatación ha sido nula. En ambos casos, se observa una mejora significativa de las prestaciones respecto a la corrosión por carbonatación.
Ensayo de penetración de cloruros mediante ensayo acelerado integral: El uso del mortero de revestimiento MORCEM ® DRY SF Plus en un hormigón referencia mejora el comportamiento respecto al inicio de la corrosión por presencia de cloruros (Dns, exp) en un 50%.
ACCIONES CORRECTIVAS: PRODUCTOS CON TECNOLOGÍA ORGANOSILANO
Las acciones correctivas son aquellas destinadas a zonas de la estructura donde ya existan daños visibles por fisuración o desprendimientos del hormigón y corrosión del acero y hemos de realizar una reparación siguiendo la metodología indicada en las normas UNE EN 1504 y el Código Estructural, que comprende los siguientes pasos:
- Eliminación del hormigón en mal estado, incluso por la cara trasera de las barras embebidas.
- Limpieza del soporte dejando la superficie rugosa y limpieza de las armaduras hasta grado SA2 ½.
- Pasivación de armaduras según UNE EN 1504-7.
- Regeneración de la sección con morteros de reparación según UNE EN 1504-7.
- Protección Superficial con revestimiento estanco al agua, el CO2 y los cloruros.
Para ello, Grupo Puma dispone de una gama de productos con inhibidores de corrosión incorporados en masa, basados en sistemas de silano multifuncionales (tecnología organosilano). Dicha tecnología se adhiere químicamente a la superficie del acero, la fase de cemento y otros materiales silíceos presentes en la matriz cementosa, es permeable al vapor de agua y reduce significativamente la absorción de agua a través de la porosidad del hormigón, confiriendo una máxima durabilidad de la zona reparada.
Inhibe la corrosión mediante fuertes enlaces covalentes con el acero (la amina organofuncional refuerza activamente la capa de pasivación del acero. Las reacciones electroquímicas en el ánodo y el cátodo se ven bloqueadas). Grupo silano protege e impermeabiliza la reparación mejorando la resistividad (la penetración de agua se reduce drásticamente en la zona reparada, reduciendo igualmente la penetración de cloruros).
La gama de productos basados en tecnología organosilano forman una capa protectora en el acero frente a ataque de cloruros, oxígeno y agua líquida. Esta capa protectora retrasa el inicio de la corrosión y/o reduce la velocidad de corrosión después de su aparición e incrementa la durabilidad de la zona reparada.

Pasivadores cementosos. Implarest C
Producto a base de cemento Portland, áridos seleccionados, polímeros con buena dispersión, y aditivos. Con inhibidores de corrosión. Protección contra corrosión de armaduras de acero en el sistema de reparación Morcemrest según la norma UNE EN 1504-7. Se puede usar en combinación con todos los morteros de reparación de la gama Morcemrest. Imprimación anticorrosión mono componente de base cementosa modificado con polímeros para la protección de armaduras. Cuando se mezcla con agua se obtiene una lechada que se aplica en el acero visto previamente saneado. Debido a su alto pH, crea una capa pasivante en la superficie de la armadura, deteniendo el proceso de corrosión.
Morteros de reparación estructural Morcemrest SR 50 Q
Mortero de reparación R4 a base de cementos especiales, áridos seleccionados y aditivos, reforzado con fibras, monocomponente, de alta resistencia para grandes espesores. Formulado con cemento sulforresistente y con inhibidores de corrosión. Apto para espesores de 5 a 50 mm en capa vertical y hasta 100 mm de espesor en capa horizontal. Tixotrópico. Proyectable. Fraguado normal.
Morcemseal todo 1
Mortero de reparación R4 a base de cementos especiales, áridos seleccionados y aditivos, reforzado con fibras, monocomponente, de alta resistencia para espesores medios. Con inhibidores de corrosión. Apto para espesores de 4 a 40 mm en capa vertical. Tixotrópico. Fraguado rápido (inicio de fraguado en 40 minutos). Pintable a las 4 horas.
Morcemseal fast todo 1
Mortero de reparación R4 a base de cementos especiales, áridos seleccionados y aditivos, reforzado con fibras, monocomponente, de alta resistencia para espesores medios. Con inhibidores de corrosión. Apto para espesores de 4 a 40 mm en capa vertical. Tixotrópico. Fraguado rápido (inicio de fraguado en 10 minutos). Pintable a las 4 horas.